For production of technical ceramics, aluminum oxides, zirconium oxides, silicates and silicon carbides are key materials.
Technical ceramics are used in the applications for metalworking, electronics, automotive engineering, medical technology, optical technologies, ballistics and many more.
Aluminum oxide is and will become the most widely used ceramic high-performance material and is used as wear and corrosion protection in plant construction, as well.
The production of finest powders sets highest demand on machinery and equipment for fine grinding and classifying, in particular on wear protection, fineness, low contamination.
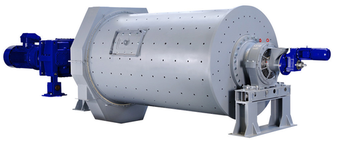