Rare earths as a component of neodymium-iron-boron alloys (NdFeB) or samarium-cobalt alloys (SmCo) are used to produce magnets that are used in electric motors, among other things. They therefore play an important role in electromobility, but also in aviation, wind turbines and medical technology. The performance of the magnets depends crucially on the quality of their ingredients. Optimised processing of the rare earths is particularly important here, and Hosokawa Alpine has developed the ideal process for this.
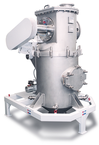